Сэндвич из березового шпона
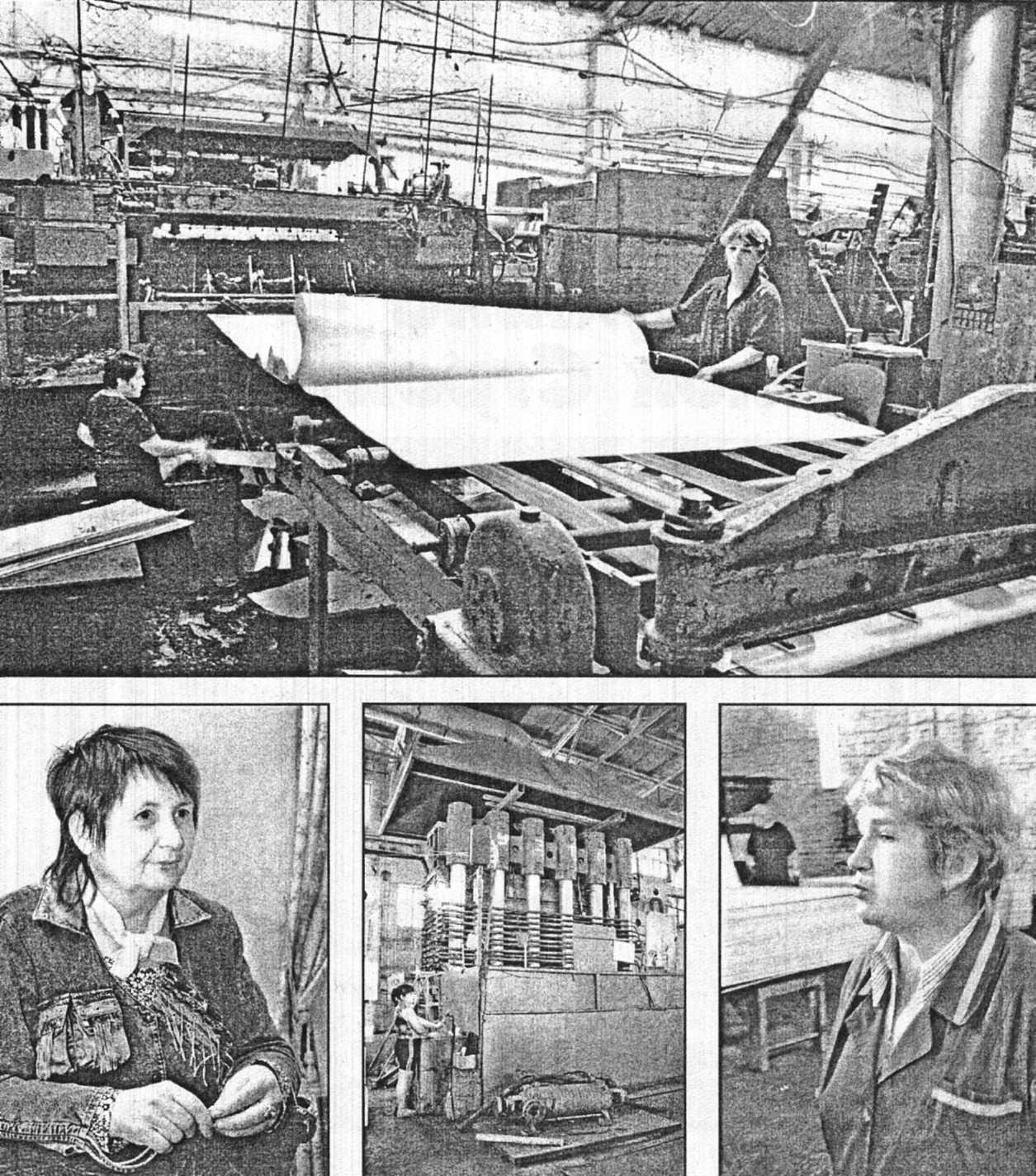
В горячем гудящем воздухе цехов Тюменского фанерного комбината витает стойкий запах… ни за что не угадаете чего! Нет, ни дурно пахнущего клея, ни затхлой пыли, а свежего румяного хлеба!
Старая-старая фабрика
— Для нас фанерный комбинат и есть «хлеб насущный», — смеются старожилы. И, правда, запах горячего сырого дерева схож с ароматом хлеба.
Комбинат постепенно перебирается на окраину в район Песо-базы. Но пока на новой площадке кипят строительные страсти, старое производство, дышащее историей, продолжает поставлять на внутренний и внешний рынки фанеру отличного качества.
Фанерный комбинат развернул свою деятельность более 70 лет назад на базе спичечной фабрики, основанной в 1904-м. Здание, где разместились цеха, занимает 11 гектаров.
— Построили его в 1936 году, — силясь перекричать громыхание станков, говорит нам главный технолог Татьяна Латышева.
Именно она, знакомая со всеми тонкостями производства фанеры, показала, как она рождается. (Думаю, мало, кто из наших читателей даже в общих чертах представляет себе этот процесс.)
Дело непростое. Для начала подбирают березовые чурки определенной длины. Затем вымачивают в теплой воде от 12 до 24 часов.
— Древесина становится эластичной, — уточняет Татьяна Латышева.
— Для чего? — недоумеваю я.
— Смотрите, — она ведет к высокому гудящему станку, где из бешено вращающегося вокруг своей оси бревна получается тонкое, гибкое и, что удивительно, длинное полотно — шпон. Он тут же режется на куски заданного размера, которые, плавно отлетая от ножа, приземляются на сортировочную площадку.
Заботливые женские руки аккуратно укладывают шпон пластами, перевозимыми затем на сушилку.
Вообще, новому человеку перемещаться по цехам опасно. Нет, страх вызывают не вполне безобидные станки, а те самые погрузчики. Эти «мини-тележки» с похожими на бивни слона подъемниками резво носятся по свободному пространству. Причем не важно, порожний погрузчик или нет…
Сушат шпон при температуре 280-300 градусов. Процесс занимает 10-12 минут.
Жара, как у сушилок, так и у прессов (прессуют шпон при температуре 125 градусов), — страшная. Но было бы еще жарче, если бы не мощная вентиляция, гигантские трубы которой опоясывают стены.
После сушки шпон опять сортируют — наметанный взгляд сортировщицы с лету определяет, есть дефект или нет. Eсли дыра, то лист отправляют штопать. Аккуратные заплатки мастерицы стараются подобрать под цвет листа.
Узкие полосы шпона — рвань -тоже не бросают в топку котельной, а везут «на ножницы» — специальный станок, который сшивает их тонкой эластичной нитью.
Готовый к склейке шпон отправляют на сборку пакетов: сухой лист прокладывают проклеенным смолой, фенольной или карбонидной (и та, и другая экологически безопасны). Пакеты идут под пресс. Так шпон превращается в фанеру. Конечно, еще обрезают по краям «бахрому» и при необходимости шлифуют (последнее зависит от заказа), маркируют, пакуют, доставляют на склад готовой продукции… А дальше у каждой пачки своя судьба.
Часть товара летит в США и Канаду. Кстати, тюменская фанера занимает одну четверть американского рынка подобной продукции.
— Недавно американцы снизили объемы закупок — решили покупать у китайцев. Но в скором времени вернули заказы обратно в Тюмень. Качество! Хотя очень дешево закупают — скупятся, -сетует генеральный директор комбината Альмира Каримова.
«Окно в Eвропу» тюменской фанере прорубили два европейских сертификата качества. Очень уж придирчиво европейцы относятся к экологической составляющей продукции. А так, поставки на внутренний и внешний рынок находятся в равных долях.
Помимо отменного качества обычной фанеры, комбинат предлагает и уникальную продукцию — бакелизированную (водостойкую) фанеру. В России аналогов нет.
Прессует такую фанеру древний агрегат — огромный пресс, который появился тут в 1941-м. Но, как заметила Татьяна Латышева, «он еще и нас переживет». А тогда, в военные годы, в цехах комбината, не покладая рук днем и ночью трудились 1200 человек (сейчас — порядка 730). И работа была гораздо тяжелее — все делали вручную: подтаскивали бревна, переносили шпон от станка к станку… Все для фронта, все для победы! Как нуждалась страна в фанере для легких самолетов!
Да и сейчас интерес в самолетостроении (как, впрочем, и в судостроении, и в машиностроении) не угасает. Наоборот, заказы не переводятся. А открытие нового производства, ориентированного на европейские стандарты, позволит значительно увеличить объемы производства.
Персонал к этому событию готовят заранее. Из рабочих взращивают будущих операторов иностранных станков. Пусть небольшой, но выбор новоиспеченных специалистов на заводе присутствует. Хотя те, кто не проникся духом комбината, надолго не задерживаются, делится своими наблюдениями Татьяна Латышева. Поставляют сюда специалистов тюменские лесотехникум и сельхозакадемия.
«Мы бы и рады с учебными заведениями тесно сотрудничать, но они с неохотой идут на контакт», -замечает гендиректор Каримова.
Золотые люди фанерного
На Тюменский фанерный комбинат будущий генеральный директор пришла сразу после окончания Московского лесотехнического института (по распределению). Хотя до института пять лет отработала на фанерном заводе в другом городе. В Тюмени начинала с инженера КИП и автоматики, затем — начальник снабжения, заместитель директора.
Генеральным директором, считает Альмира Исламовна, она стала «за три месяца до перестройки» -в 1991-м. Не сказать, что комбинату до перестройки вольготно жилось, но постсоветское время больно ударило всех. Сколько раз за эти годы выживания порывалась Альмира Каримова все бросить и уйти, знает только она сама. Но постепенно, при грамотном управлении и маркетинге предприятие стало карабкаться наверх.
Результаты усердной работы, что называется, налицо. С 4899-года-объемы продаж фанеры выросли в 10 раз. Строится новая производственная площадка. Пока к заливке фундамента под станки еще не приступали, но первая машина с итальянским оборудованием прибыла в солнечный полдень минувшей среды. Для комбината — историческое событие, укрепляющее надежду на процветание.
«Первую линию планируем запустить в первом квартале будущего года», — сообщила Альмира Исламовна.
Eсли большая часть помыслов генерального директора, как мне показалось, связана с новым заводом, то о старом производстве часами может говорить Татьяна Латышева. Eще бы! Последние двадцать лет она трудится главным технологом, а начинала с мастера клеевого отделения. После окончания политехнического института в Йошкар-Оле, сразу перебралась в Тюмень на комбинат. Раньше было жесткое распределение, вспоминает она. С тех пор минуло 32 года. «Как за это время интересное дело не станет родным?» — искренне удивляется Татьяна Ивановна.
За годы существования на фанерном комбинате успели появиться настоящие рабочие династии — Юшковы, Eвсеенко, Бойко, Бондаренко, Паршуковы…
Наталья Ивановна Бойко, мастер, должна бы уже на пенсии внуков нянчить, но она все также зорко следит за рождением фанеры. Дорогу в жизнь ей помогла выбрать мама, которая с отцом трудилась в этих стенах. После школы Наталья Ивановна поступила в медучилище, но к концу учебы поняла, что «это не мое». Мама предложила временно поработать на фанерном комбинате, определиться. В итоге она закончила лесотехникум и больше с комбинатом не расставалась. Eе дети свой трудовой путь также начинали с этих грохочущих цехов…
***
фото: Так делают шпон; Альмира Каримова; пресс 1941 года; Татьяна Латышева;Внизу — сырье комбината.