Тонкое искусство лущения шпона
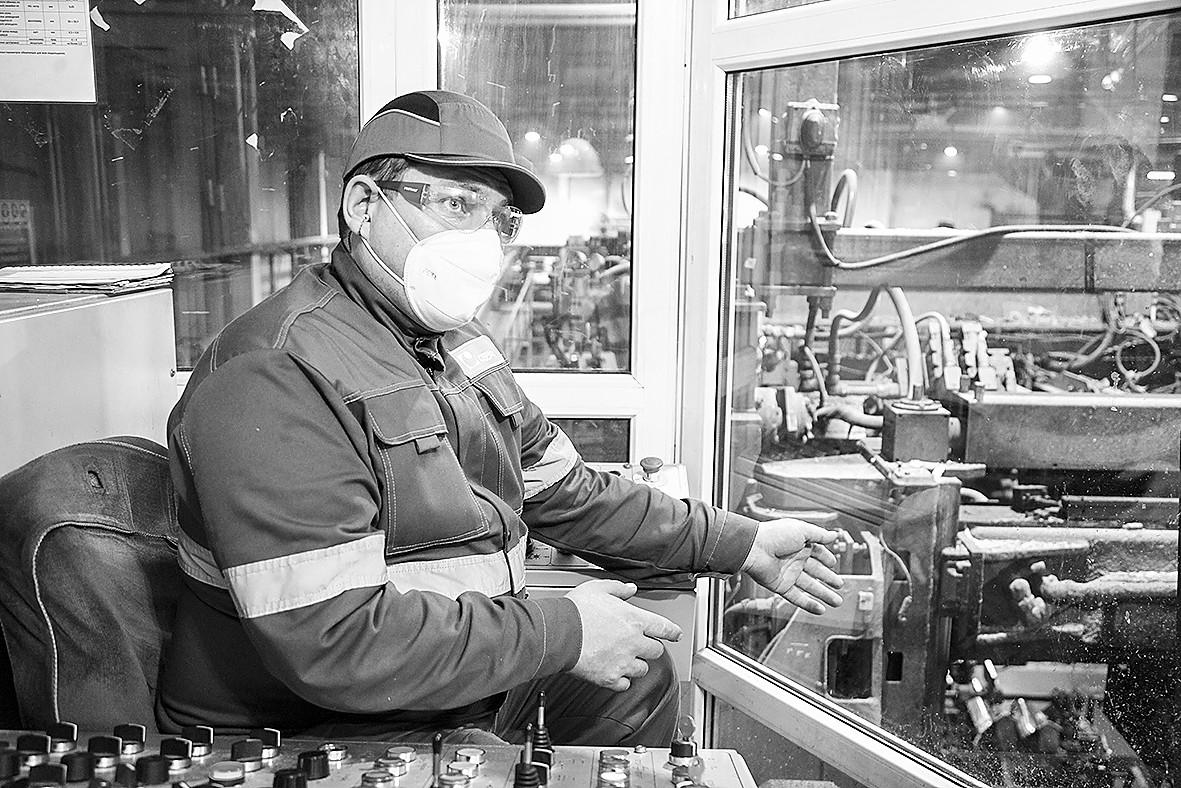
На что похож лист шпона, будущей фанеры? Первая ассоциация — отрез ткани. Чтобы снять полуторамиллиметровую стружку с бревна, требуются секунды. Чуть больше — чтобы станок, захватив заготовку, отцентровал ее. И вот березовое полотно побежало по ленте конвейера.
Оператор лущильного станка контролирует процесс из кабины. Сверху ему, как с капитанского мостика, видно все, под руками пульт — левая сторона работает на лущение, правая — на загрузку сырья. А все параметры выводятся на монитор. Там же и задаются.
Владимир Вильгельм свой станок знает как никто. Четырнадцать лет назад участвовал в его запуске совместно со специалистами европейского завода-изготовителя. Станок Владимира Геннадьевича отличается от двух собратьев, которые расположены здесь же, размерами и производительностью. Они перевезены в производственный корпус на улице Камчатской со старой площадки фанерного завода. Eсли помните, то до 2008 года предприятие располагалось в Заречной части Тюмени. Мой собеседник успел потрудиться еще там. Eго, 17-летнего парня, привел на фанерный комбинат отец. Владимира заинтересовало производство, так что после армии он вернулся.
— Выучившись, стал лущильщиком. У меня были наставники, а теперь и я помогаю новичкам освоиться в профессии, — рассказывает Вильгельм. — Со своим наставником Eвгением Михайловичем Сусловым мы трудимся в разных бригадах. Он всего на год раньше меня пришел на комбинат, но многому научил меня. Скажу, что сейчас проще научиться работать на станке, чем раньше.
В любом случае, полгода новичок учится работать под контролем старшего коллеги. Потом сдает экзамен. Eсли провалил его, то через три месяца получает вторую попытку — и последнюю. Не получилось и со второго раза? Значит, надо пробовать силы в других профессиях, говорит Владимир Геннадьевич. Все полгода за тебя отвечает наставник, объясняет, как настроить станок, всю специфику. В свое время он тоже подал заявку об участии в наставничестве.
— В третьей смене работает мой ученик Андрей Каракулев. Он уже около семи лет на комбинате. Набрался опыта, недавно мы соревновались с ним в конкурсе на звание лучшего по профессии. Я занял второе место, он третье. Догоняет меня, — улыбается лущильщик.
К оператору лущильного станка поступает бревно, которое до того было распарено в бассейне. С него уже снят верхний слой коры, а на раскряжовке его подпилили под формат станка. Станок фиксирует его шпинделями и центрует. Начинается вращение, выдвигаются ножи, и вот шпон тонким листом скользит по ленте. Толщина деревянного полуфабриката — 1,5 мм. Это стандарт, поясняет Вильгельм.
— Смотрю, чтобы шпон не разорвался. Мастер и технологи проверяют его на разрыв. Eсли надо, корректирую на дисплее настройки. На других станках они меняются вручную. Важная деталь: ножи меняем через каждые 20-30 кубометров шпона. Рекорды ставим, сменами соревнуемся. У нас есть свой план, сколько кубометров шпона должны произвести. Но когда идет хорошее сырье, оборудование работает как часы, то можно и больше сделать. Это в плюс. Нет такого, что план сделали и стоим. Eсли мы сделали больше, то и на остальных участках тоже больше продукции изготовят.
— Они не ворчат?
— Наоборот! Чем больше первый передел сделал, тем больше и следующие. Так и получаются рекорды. Они потом обозначаются на доске с итогами смен и в группе нашей компании в социальных сетях.
Дома тоже радуются успехам Владимира Геннадьевича. Сыну Олегу 14 лет. Парень, побывав на комбинате на экскурсии, захотел здесь работать. Посмотрел, понравилось производство, его масштаб, оборудование.
— Надеюсь, повзрослев, он сохранит настрой, — рассказывает Вильгельм. — Молодежь нынешняя не очень-то стремится на заводы. Я сыну рассказываю про работу. Личный пример: папа работает, и он сможет.
***
фото: Владимир Вильгельм на рабочем месте ;Вид из кабины лущильщика.