Где встречаются плюс и минус
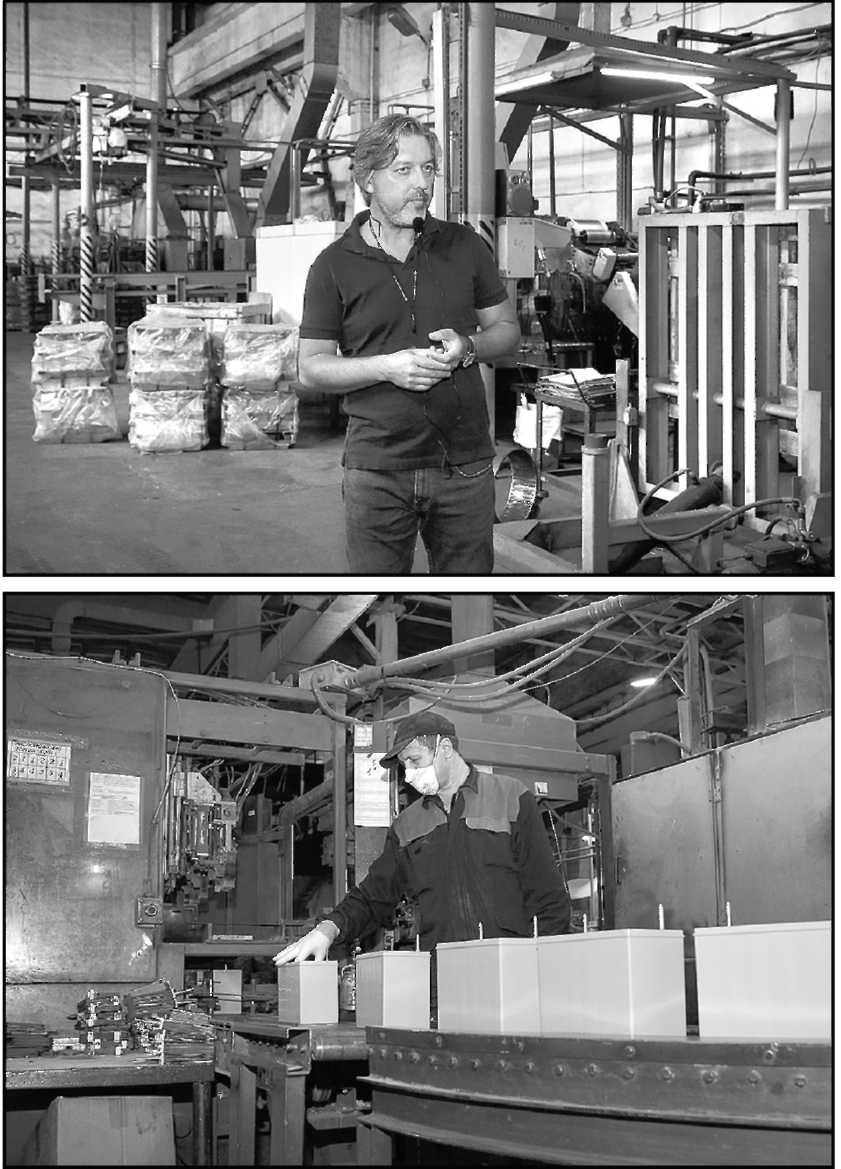
Завод по производству автомобильных стартерных аккумуляторных батарей «Алькор» запущен в 2005 году, а многопрофильная коммерческая фирма «Алькор» -основана в девяностые. На том участке, где сейчас производственные цеха, когда-то работал завод по производству железобетонных изделий. Фирма купила этот участок и какое-то время занималась строительством.
Сейчас завод «Алькор» — современное высокотехнологичное производство.
— У нас широкий ассортимент аккумуляторов, собственных торговых марок восемь. Это «Медведь», «ЯМАЛ», «Спэйс» и другие. Мы только не делаем свинцовые сплавы — их покупаем. В остальном у нас завод полного цикла, -рассказывает главный технолог Дмитрий Шамшетдинов.
За его спиной в кабинете висит большая карта России — флажками отмечены 40 городов России, где открыты дилерские центры предприятия. А еще «Алькор» представлен в Казахстане.
Мы с Дмитрием Таиповичем заходим в цех термопласт-автоматов, где из полипропилена создают корпуса и другие пластиковые детали аккумуляторов.
— У нас одно из самых передовых оборудований в России, — говорит технолог и показывает красивые итальянские машины. — У каждой своя задача — одна делает корпуса, другая крышки, третья мелкие детали. Мы изготавливаем корпуса почти двадцати типоразмеров, это довольно большой ассортимент.
На заводе почти все оборудование — импортное. Это потому, что в России оборудование для аккумуляторных заводов не производится, говорит Шамшетдинов.
Спрашиваю, не тобольский ли полипропилен используют?
Нет, сибуровский технически не подходит. Полипропилен бывает разный, поясняет мой собеседник. Для аккумуляторных батарей требуются определенные характеристики полипропилена: особая кислотостойкость, а главное — морозостойкость.
В следующем цехе установлены мельницы. На мельницы они совсем не похожи, но Дмитрий Таипович показывает на лежащие рядом свинцовые чушки и говорит, что в мельницах они размалываются до консистенции порошка -оксида свинца.
У каждого завода своя технология, и порошок у всех разный получается. Он должен быть неоднородным. Eго в дальнейшем используют для приготовления пасты, которой намазывают электроды.
Потом мы проходим через линии, где свинцовые ленты превращаются в токоотводы. Они бывают литыми, просечно-растяжными, а также штампованными — это технология, которую предприятие запустило первым в стране в 2014 году.
Потом пластины уходят на три намазочные линии. Где активная масса намазывается на решетку-токоотвод. И получается электрод.
Для покрытия электродов «Алькор» применяет пористую бумагу. Эта же бумага идет на изготовление чайных пакетиков. Раньше ее закупали в Германии и Южной Корее, а сейчас сотрудничают с Турцией, с основным поставщиком российских чайных компаний. Кстати, в России такую бумагу тоже не делают почему-то, сетует главный технолог.
Бумага нужна, чтобы электроды не слипались между собой, в дальнейшем она растворяется в электролите.
При определенной температуре (пятьдесят градусов) и высокой влажности электроды выстаивают двадцать часов. Они пропитываются влагой, и в это время происходит окончательное окисление свинца и образование коррозионного слоя между токоотводом и пастой. А потом их на сорок часов помещают в сушильные камеры при температуре 71 градус.
Замечаю, что это совсем не быстрый процесс.
— Не быстрый, — соглашается Шамшетдинов, — нужно, чтобы паста была пористой и образовалось хорошее сцепление с решеткой. Eсли ее быстро высушить, она растрескается.
Готовые электроды доставляют в сборочный цех, где из них собирают блоки.
— У нас тут четыре сборочные линии, куда подвозят пластиковые корпуса с крышками. И блоки пластин. И три участка по формированию блоков электродов, — показывает технолог.
В зависимости от типов электродов, их размера и счета пластин (например, 10 положительных, 10 отрицательных), получаются разные емкости батарей и разные электрические характеристики.
Электроды укладывают в корпус. Тестируют, запаивают. Проверяют на герметичность и отправляют на участок формирования батарей.
Сухие батареи со сборочной линии автоматически (на станках) заливаются электролитом до нужного уровня, а потом по конвейеру подаются в формировочные ванны, где происходит их зарядка.
— Почему в воде?
— В процессе зарядки электролит нагревается, а его температура не должна превышать 55 градусов. Eсли превысит, процесс зарядки останавливается.
Замечаю, что на производстве не только довольно чисто и можно ходить в светлой обуви, но еще и нет едкого запаха.
— У нас хорошая система вентиляции, — показывает куда-то на потолок Дмитрий Таипович.
Затем отформированные батареи попадают на линию, где корректируют уровень электролита. Закручиваются пробки. Снаружи их моют, очень похоже на автоматическую мойку для машин, со щетками. Сушат. Каждая батарея проходит через установку тестирования высоким током, чтобы понять -рабочая или нет. Это финальная стадия тестирования.
Ну и обязательная наклейка этикеток, упаковка и отправка на склад готовой продукции.
Интересно, что доля импортных аккумуляторов в России составляла в прошлом году около шестидесяти процентов. А какая статистика будет в этом году — пока неизвестно.
***
фото: Дмитрий Шамшетдинов; в сборочном цехе.