Заводу есть куда расти
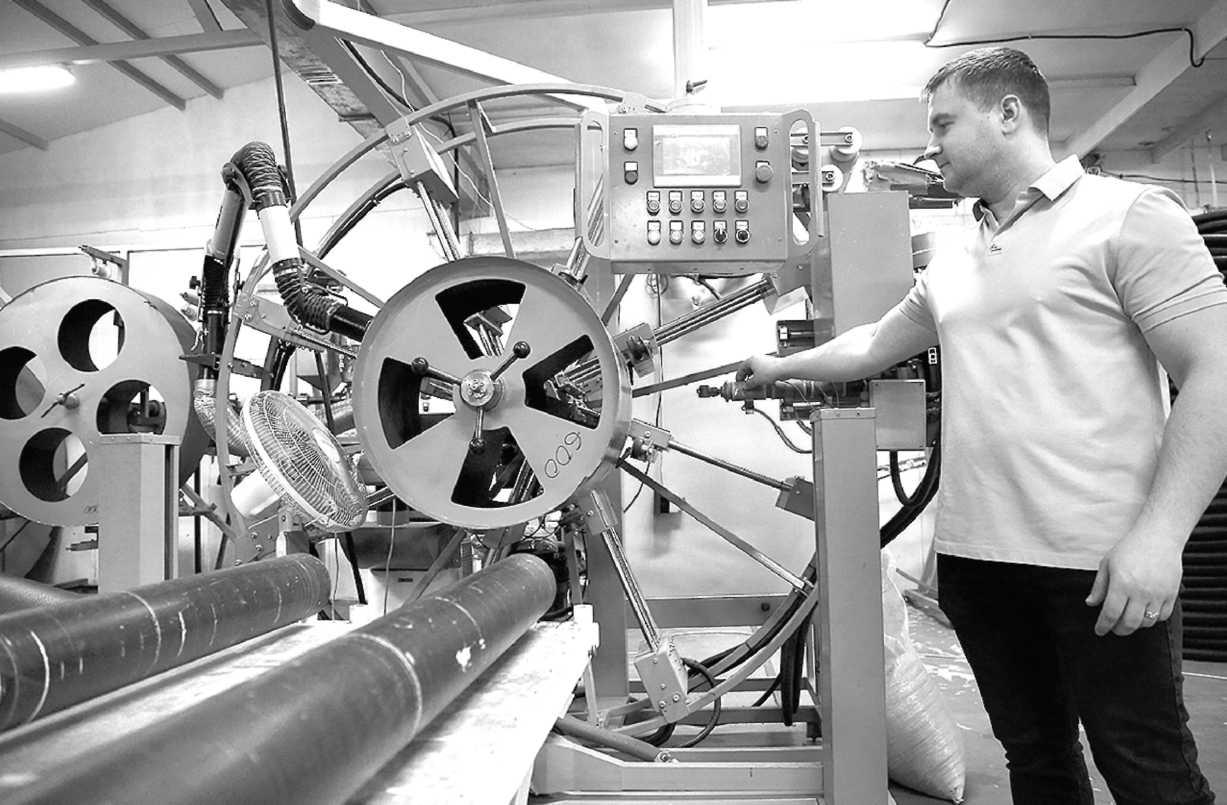
Система сбора и отвода ливневых стоков с применением дренажных фильтрующих колодцев производства Тюменского завода гофротруб широко используется по всей стране, в Тюмени установлено более двухсот точек. Калининская управа, например, монтирует ее при благоустройстве дворовых территорий. Она эффективна там, где нет возможности протянуть централизованную ливневую канализацию.
Eсли у вас во дворе каждый раз после дождя натекает большая лужа — вот тут-то и ставят систему. Стоки через решетку попадают в дождеприемник (герметичную емкость под землей), а оттуда по переливному трубопроводу в дренажные фильтрующие колодцы. В них есть фильтрующий элемент, который очищает ливневые стоки от вредных для почвы нефтепримесей (масла, бензин). Это важно, потому что дальше очищенные стоки попадают в грунт. Первый колодец установили в 2017 году в Восточном округе на улице Олимпийской — и он работает. Для обслуживания системы достаточно провести ревизию и в случае загрязнения очистить дождеприемник. Можно вручную (емкость всего полутораметровая), а можно илососом.
Завод стал резидентом Сколково с прошлого года — с проектом системы сбора, очистки и отвода ливневых стоков с применением дренажных фильтрующих колодцев. Теперь компания регулярно участвует в специализированных выставках (резидентам компенсируют эти затраты). Директор Виталий Федорищев рассказывает, что выставки дают возможность найти партнеров, продвигать продукцию, заходить в новые проекты. Производство пока одно — в Тюмени, но в планах открыть еще и в других городах. И выйти на всероссийский рынок.
Виталий Анатольевич показывает цех завода — экструдер, на котором делают гофрированные трубы. Труба получается из мелких гранул полиэтилена низкого давления — это отходы, вторичное сырье и отходы собственного брака. Все пускают в оборот — безотходное производство.
Гранулы полиэтилена подаются в бункер, нагреваются, плавятся, и выходит экструзия, которая попадает на ребристый формовщик, а на выходе получается гофротруба.
Кроме этой линии, в цехе есть еще три. И все — на станках собственного производства. Мне показывают оранжевый станок, разработанный при поддержке департамента инвестиционной политики и государственной поддержки предпринимательства Тюменской области, грант получили в 2021 году, взяли на работу конструктора, сделали бизнес-план. Станок — автоматический, что очень удобно, достаточно ввести нужные параметры (диаметр, длину) и вовремя загрузить трубу и гранулы в емкость. Процессы оптимизировались, а объем производства вырос. Поэтому в прошлом году расширили площади, насколько это возможно, сделали пристрой.
На станке техническая труба из полиэтилена низкого давления навивается на барабан — а экструдер, похожий на клеевой пистолет, склеивает трубы между собой. Это герметичный вариант — он для труб и септиков, а есть дренажный — из гофротрубы для дренажных систем и ливневых канализаций.
Мастер Александр Попов с ручным экструдером для сварки склеивает детали плавучих модулей -да, готовые герметичные трубы можно использовать для создания пирсов, — этот заказ уедет на озеро в деревне Иваново Армизонского района Тюменской области.
— Мы придумали и изготовили собственный катамаран, зарегистрировали его как маломерное судно в ГИМС. Летом используем. Мы представляли этот плавучий модуль в 2022 году на выставке «Тюменская марка» и стали победителями, — рассказывает Виталий Федорищев.
На станок и всю продукцию компания получила патенты и сертификаты. Хотели бы создать новую производственную линию, чтобы модернизировать станок на больший диаметр. Но существующего цеха для этого мало.
— Сейчас ведем переговоры об аренде участка в Горьковке, — объясняет Виталий Федорищев.
Учредитель компании Виктор Перекрестов считает, что с земельными участками промышленного назначения непросто. В индустриальных парках есть условия, которые малое предприятие выполнить не сможет.
— Большими компаниями становятся, начиная с маленьких. Нам бы хватило участка в один гектар. Сейчас нам негде складировать продукцию. Нам хотелось бы расти, спрос есть. Чего не хватает промышленникам? Нам нужна земля. А еще надо изменить подход к выделению финансовой помощи. Заем меньше 50 миллионов взять невозможно, а если нам столько не надо? Их же надо вернуть потом, — сетует Виктор Владимирович.
— Как вы стали заниматься гофротрубами?
— Когда только начиналось строительство коттеджных поселков, мы занимались благоустройством, облицовывали дома камнем. И совершенно случайно в 1998 году заказчик пожаловался, что его участок затапливает. Сможете, говорит, решить проблему водоотведения? Мы ответили: сможем. Никогда не надо отказываться! Eсли есть запрос, надо его изучить. Любую проблему решают люди — если у кого-то получилось, то и мы сможем тоже. Вот так мы нашли свою тему. Сначала было сложно. Мы нашли информацию про водоотведение, никто тогда даже не слышал про лотки. Фирма наша тогда назывались «Вернисаж» (нас до сих пор знают под этим названием). Стали искать трубы и использовать их в работе. И в процессе решили упростить и удешевить технологию. Eсли ты будешь конкурентоспособен — значит, у тебя будет больше заказчиков. Мы купили линию гофротрубы, и грянул кризис 2008 года. Нам одобрили кредит, а доллар прыгнул. Линия китайская. И мы все равно заказали. Потом пришла идея делать колодцы, сделали первый станок сами. Сначала отрабатывали систему на частных участках, а потом предложили муниципалитету. Это не просто колодец, а система. Вот сейчас муниципалитеты в своих проблемах подтопления применяют нашу технологию — все вытекло из тех лет, из опыта.
— У вас не так много сотрудников.
— Хороший вопрос. У нас на сегодняшний день пятеро рабочих, они способны обеспечить всей продукцией нашу область, потому что оборудование, которое мы разработали, автоматизировано. Не надо смотреть на численность, лишь на показатели роста. Мы растем.
НА СНИМКАХ: директор Виталий Федорищев; мастер Александр Попов.
Фото Виктории Ющенко