Штамповка деталей приносит людям радость
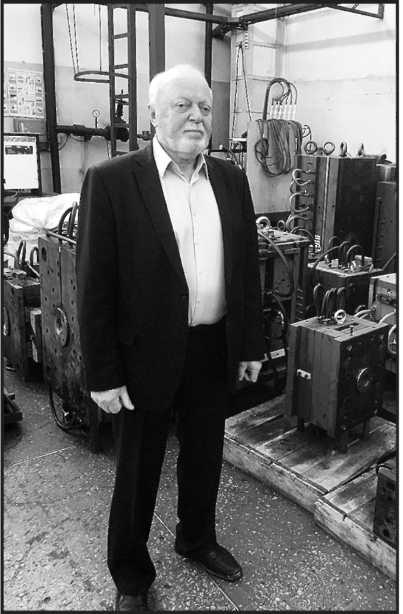
Это сейчас переработка пластика в тренде, а компания «Расавит» начала ею заниматься еще пятнадцать лет назад. Теперь это самый крупный переработчик от Урала до Владивостока, участник конкурса «Тюменская марка».
Лет 25 назад перед Тюменским аккумуляторным заводом встал вопрос обеспечения предприятия сырьем, в том числе и полимерными материалами, из которых делаются внешние детали аккумуляторов — крышка, корпус, ручка. Директор завода Александр Кореляков предложил Виктору Абрамову возглавить новое производство. У бывшего завода кузнечно-прессового оборудования купили площадку в Тюменском районе — недостроенный кирпичный завод, разобрали стены, сняли перекрытия, фермы, залили фундамент, хотя на улице стоял мороз! В названии предприятия решили зашифровать реверанс в сторону инвесторов из Австрии, так появилось название «РосАвит». Затем пришлось переименоваться в «Расавит», так как проверяющие органы усмотрели в написании с буквой «о» какие-то нарушения.
Иностранные инвесторы полагали, что производство заработает нескоро. По европейским меркам на поиск подрядчика, инженерные изыскания, проектирование, согласования на строительство, монтаж оборудования уходит не меньше 3-4 лет. Но у наших производственников большой опыт становления в самых невероятных условиях и за самые короткие сроки. И всего через год на открытии Степан Киричук, тогдашний мэр города, сказал, что если бы завод не взялся за переработку пластика, то аккумуляторному пришлось бы возить комплектующие из-за рубежа.
— Раньше производство мне представлялось монотонной работой, не думал, что это будет интересно, — рассказывает директор предприятия Виктор Абрамов. — После окончания Омского политехнического института меня распределили на Тюменский моторный завод, назначили начальником отдела реконструкции гальванического, термического, механического и литейного цехов. Надо было работать с разными подрядчиками, знать производственные технологии, строительные, понимать, что такое монтаж, запуск. И думать самостоятельно. На моторном была жесткая кадровая политика: если два-три раза принял неправильное решение, сорвал сроки, потратил лишние деньги — пиши заявление. Система суровая, но простая и понятная. Судили по делам и знаниям.
Абрамов много ездил в Eвропу, изучал производство. Ставить «Расавит» на ноги помогали и инвесторы из Италии и Австрии. Позже по разным политическим и экономическим причинам иностранные инвесторы с завода ушли.
Первый год после открытия предприятия в цехах установили восемь термопластавтоматов (сейчас их 19), которые изготавливали до ста тысяч комплектов для сборки аккумуляторов. Оборудование было импортное. И сейчас таковым осталось. Только тогда — немецкого, итальянского, австрийского производства, а сейчас китайского. Но на предприятии сразу сами начали обслуживать всю иностранную гидравлику, электронику, механику. Для этого ежегодно все рабочие и инженеры проходят переквалификацию.
— Экзамены на профпригодность у нас без скидок, бывают и со слезами, — говорит Абрамов. — Расслабляться нельзя, сколько бы лет ни работал. Мы держим марку. У нас каждый рабочий имеет свой номер, который ставит на изделии, нет необходимости держать десятки проверяющих. Ничего выдумывать не надо: все системы сертификации были разработаны еще в советские времена в авиапроме. В СССР на предприятиях все было четко отработано: контроль качества, технологии, сертификация.
Когда в 1999 году создавали предприятие, в коллективе было около трех десятков человек, сейчас почти в три раза больше. Но пропорция «рабочие кадры -ИТР» сохранилась та же. На «Расавите» каждый пятый с инженерным образованием. Это необходимо, чтобы осваивать новые виды продукции (сейчас в ассортименте уже 800 наименований).
Много лет здесь занимаются рециклингом — вторичной переработкой пластика. В год из 3500 тонн вторичных полимеров, которые уехали бы на свалку, получают около 3000 тонн высококачественных полипропиленовых и 50 тонн полиэтиленовых гранул. С 2005 года на участке рекуперации переработана почти 31 тысяча тонн полимеров и произведено более 27 тысяч тонн вторичной гранулы. Предприятие является крупнейшим производителем и поставщиком этой продукции за Уралом. Из гранул в литейном цехе предприятия штампуют разнообразную продукцию — от колпачков до ящиков и поддонов. Используется российская технология возврата вторичных полимеров в производство. Оборудование работает 24 часа семь дней в неделю.
— У наших работников понятие выходной относительное, — говорит Абрамов. — Eсли потребуется консультация, специалисту могут позвонить хоть ночью. Поэтому, когда принимаем новичков на работу, с каждым беседую, чтобы понять, наш ли это человек, способен ли он трудиться не только за деньги, но и за идею. Но отношение к идее должно быть позитивным. Для меня профессиональное счастье — не должность и не карьера, а то, что я по-прежнему рад приходить утром на завод.
***
фото: Виктор Абрамов;Литейщица Ирина Кирилюк у контейнера с гранулированной массой;Литейщица Светлана Ситникова сортирует готовые детали