Хорошо смеется тот, кто умеет работать
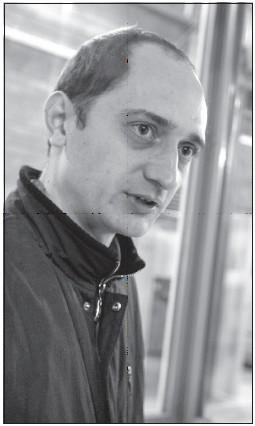
На Тюменском аккумуляторном заводе запустили новый цех, аналогов которому нет ни в России, ни в странах СНГ. Теперь в Тюмени производят полиэтиленовые сепараторы для аккумуляторных батарей.
Как говорит директор завода Александр Кореляков, это одна из широко распространенных и модных на сегодня технологий. Раньше аккумуляторному приходилось закупать сепараторы за границей: в Европе, в Южной Корее… Одна только транспортировка сколько времени занимает! И партнеры не всегда обязательны. Два года назад сорвались поставки из США, и аккумуляторный завод сорвал заказ в свою очередь.
Тогда и решили, что надо создавать собственное производство сепараторов, чтобы ни от кого не зависеть. Участок организовали на месте бывших цементных складов на территории завода.
Когда на конгрессе «Евробат-2008» в Варшаве представители нашего завода сообщили, что планируют наладить у себя производство полиэтиленовых сепараторов, в зале зазвучал смех. А в прошлую пятницу торжественное открытие цеха, в появление которого на «Евробате» не поверили, состоялось.
Начальник цеха Алексей Разинков через огромную территорию завода ведет нас на экскурсию по новому производству.
— Давайте заглянем по пути, я покажу, как используются сепараторы в аккумуляторных батареях, — предлагает Алексей Александрович.
Тонкие серые рифленые пластинки с неприятным запахом — это и есть сепараторы. Они предназначены для разделения положительных и отрицательных электродов в батарее.
Посмотришь, как выглядят, — ни за что не поверишь, что их производство — самый сложный процесс, с которым пришлось столкнуться на практике Алексею Разинкову, инженеру, выпускнику нефтегазового университета, в прошлом — конструктору.
— Производство начинается с завоза сырья: сверхвысокомолекулярный полиэтилен, белая сажа, индустриальное масло, технический углерод, — рассказывает Алексей Александрович. — Сырье поступает в экструдер, где его смешивают, пропускают через специальный раствор и разделяют на гранулы. При этом нужно, чтобы все компоненты смешивались в строгих пропорциях и определенной последовательности.
Черные нити смешанного сырья похожи на резиновые. Проходя через раствор, они приобретают синеватый оттенок. Разделенные гранулы очищают от масла и пропускают через другой экструдер, чтобы получить ленту.
— А сейчас я покажу вам самое опасное место в цеху. Фотографировать там нельзя.
Алексей Александрович открывает двойную дверь в помещение, где находится емкость с гексаном.
В гексане лента очищается от масла, становится пористой, как губка, и очень прочной.
Гексан очищают от масла, которое возвращают к началу процесса. А готовый продукт уже выходит на намоточную машину. Теперь его остается только нарезать на пластинки необходимой длины.
— Кстати, намоточная машина, на которой лента скручивается в бобины, и две резочные тоже придумали и собрали у нас, — продолжает Алексей Разинков. — А вот и сами разработчики…
Поскольку производство пока еще экспериментальное, контроль авторов, это конструкторы Алексей Потапов и Даниил Решетников, необходим. Но я успеваю задать пару вопросов: — Долго работали над машинами? — Дольше, чем рассчитывали. — Как вы их придумали? А что брали за основу?
— У нас было техзадание. А в остальном — голова нам дана не для того, чтобы шапку носить, — отшучивается Алексей Потапов.
Действительно, как объяснить процесс, когда у тебя в голове прорисовываются элементы нового станка? Как ты понимаешь, каким он должен быть, чтобы удовлетворять всем пунктам техзадания?
Начальник нового цеха Разинков был прав, когда говорил, что придумать станок гораздо сложнее, чем научиться на нем работать. Найти общий язык с новой автоматизированной техникой пришлось ему и еще 15 рабочим. В основном, это молодые парни, прошедшие специальные курсы по технической безопасности. Осваивали станки опытным путем. Один попробовали запустить… Второй…
— Это очень опасно, — замечаю я, вспоминая емкость с гексаном.
— А по-другому никак. В институтах же этому не учат, — говорит Алексей.
Сейчас цех работает в опытном режиме. Наладили выпуск сепараторов для автомобильных, тепловозных и тяговых батарей, продолжают совершенствовать производство.
Александр Кореляков, директор, отметил, что открытие цеха — значимое событие для завода в свете выступления президента, который говорит о модернизации производства. Но дело не только в этом.
— Не все сразу получалось. Что-то требовало доработки, новых решений, — говорит Александр Васильевич. — Например, в новом производстве применяется азот. Мы рассчитывали, что закупленного газа хватит надолго. Но оказалось, мы «съедаем» газ очень быстро. Поэтому сейчас монтируем свою азотную станцию. Мы сделали все своими заводскими силами. Я почему вас пригласил? Может, людям будет интересно, что наши заводы не встали, что здесь что-то еще придумывают? Цех уже обеспечивает потребность производства в полиэтиленовых сепараторах на 30 процентов. А на заводе говорят о монтаже второго комплекта оборудования, который позволит обеспечить уже на 70 процентов. Даже есть желающие покупать новую продукцию у аккумуляторного завода, хотя пока она предназначена только для своих потребностей.
***
фото: начальник цеха Алексей Разинков;готовая продукция;процесс пошел.